5 Ways To Achieve Safety In Your Plant
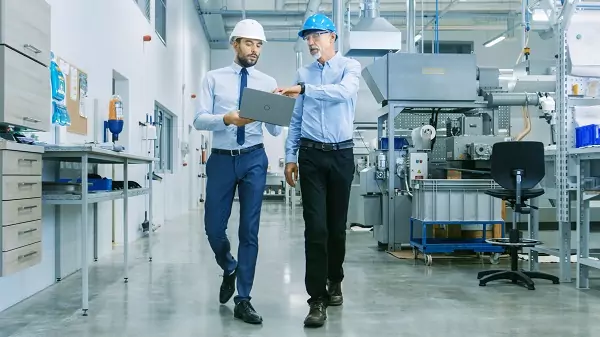
Safety has always and will be a top priority in the manufacturing industry. From physical injuries to environmental hazards, these unfortunate events could cost the company a substantial amount of resources. On top of these events, they are hard to predict which means they could strike at any time. Take COVID-19, for example, no one could scope out the damage this virus would do to the manufacturing industry leading to a negative outlook for the future with leading manufacturers – 78.3% of manufacturers anticipating a financial impact from the virus. Without a plan when these unfortunate events happen, there could be a potential to close down the manufacturing plant and much worse. Luckily, there are ways that you can convert your manufacturing plant into an atmosphere that is safe and encourages the use of standard safety practices. In this post, FasTest will break down what the most common safety hazards are and 5 ways to achieve safety in your plant.
Before we get into ways to achieve overall safety in your facility, let’s go over a few things that could happen without the proper safety measures in place:
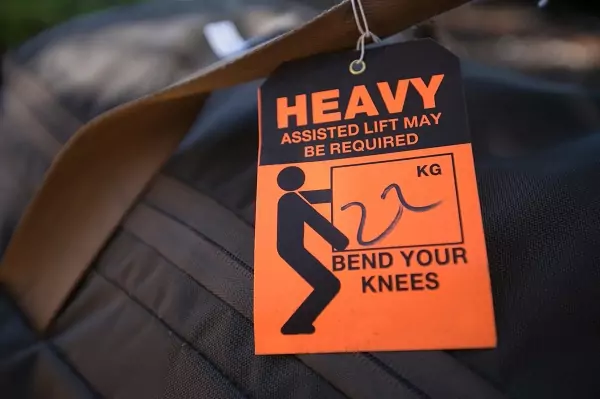
Repetitive Motion Injuries:
Repetitive stress is one of the most common injuries in a manufacturing plant. This injury is caused by doing the same motion repeatedly in a long-time frame which puts stress on the muscles, tendons, nerves, and ligaments. According to NHS, vibrating equipment usually found on assembly lines are thought to increase the chance of getting a repetitive motion injury and make the symptoms worse. Most plants will overlook repetitive motion injuries since they are very common and are not thought of as a serious injury that can put the worker in the hospital.
Lifting Heavy Objects:
Most times, employees believe that they can lift more than they can handle. This can lead to serious injuries, sometimes fatal. To make sure this doesn’t happen in your plant, post signs around objects that may be heavy, IE. Loading docks or inventory storage. Also, continue to include the “find a buddy to help” tactic in HR presentations and monthly meetings with floor workers.
Connectors Blowing Off During Testing:
To assure the quality of the products you manufacture, you need your plant to participate in effective and safe leak testing. Without the proper connectors, you risk pressure blowouts which leads to serious injuries. Not only can pressure blowouts cause injury, but there is also potential to cause environmental harm.
Slips and Falls:
Even though this one could probably be the easiest to avoid compared to other safety hazards in the plant, slips and falls affect everyone and could be extremely harmful. There are some simple fixes to this issue such as requiring non-slip shoes on the plant floor and wet floor signs placed whenever the floor may be slippery.
Now that we have gone over a few things that could happen in your plant without the proper safety measures, here are five ways to achieve safety in your manufacturing plant:
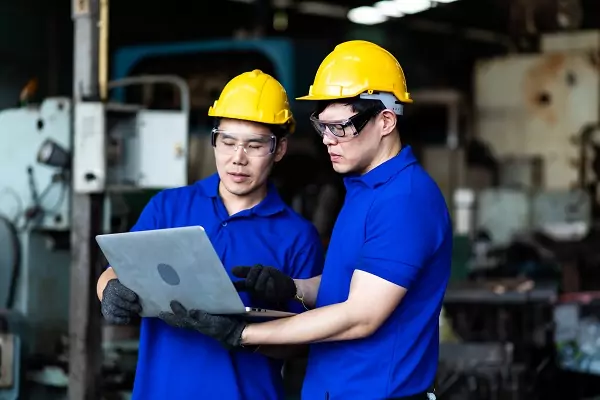
1. Follow Universal Safety Documents
2. Start it at HR
3. Implement Safety Measures
Repetitive motion stress is one of the leading workplace injuries. A great way to prevent them is to ensure that your workers take periodic breaks during their shift and are not doing the same motion for long hours. Evaluate with your plant managers and overseers to ensure that they are watching out for the employees and correcting their behavior that might lead to serious injury.
Another tactic to improve safety in your plant is to cross-train employees so they can switch what they’re working on periodically. This is a great way to reduce the chance of repetitive motion injury. Along with the safety measures, cross-training your employees provides many different benefits to your company, plus it will increase worker engagement as they get to learn a new job or maybe a new skill.
4. PPE
PPE or Personal Protective Equipment is vital for safety in the plant. PPE protects workers from different objects that might harm them including Metal shavings, sparks, heat, and much more. Offer PPE products across the plant and in easy to find places. Educate the user of the values of PPE, not from the financial standpoint, but how it impacts their lives when an incident occurs. A safe workforce is a happy workforce.
5. Connectors
Injuries can happen anywhere but high-pressure applications should be handled with special attention. The most common safety concern for tool connections is if they disengage under pressure. Connectors need to be properly designed to handle the test parameters. FasTest has a broad offering to handle most any connection and has experts willing to help your company create a safe environment.
Safety is important for the health of your company and keeping your plant operational. Accidents happen all the time and are very unpredictable (take COVID-19 for example). By implementing these five strategies into your plant safety plan, you’ll be better able to prepare and potentially avoid most incidents. Learn more here on how FasTest can create safe leak testing in your manufacturing plant.
Connect with FasTest: Twitter • Facebook• LinkedIn
For additional FasTest products or information, contact:
1-800-444-2373 • www.fastestinc.com • marketing@fastestinc.com